Starmatik Solutions
Remote Robot 1.0
Remote
Robot allows manual/automatic control of a 6/7 axis industrial robot, up to 500 kg payload, performing real-time collision detection between the
robot and a simulated environment for a real safe-motion.
The driving hardware consists of two heavy duty, hall sensor proportional joysticks, each of them with three axis control and dual button switches.
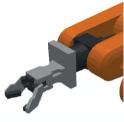
A touch screen monitor allows quick access to the software functions, like device configuration, mode selection and positioning of the virtual camera in the simulated environment.
It is also possible to drive and monitor the
robot digital I/O in order to interact within the surrounding environment (e.g. picking an object with the gripper, having an immediate feedback on the applied force).
Virtual Safe Control
The virtual environment displayed on the Remote
Robot console allows to freely choose the point of view, enabling the operator to look at the robot with the best preferred perspective, otherwise unconfortable or even unaccessible.
A number of networked real time video cameras are also directly accessible from the Remote
Robot graphical interface, together with a special driving mode that enables the operator to move the
robot with respect of the current camera camera perspective or using the current simulation environment point of view.
Path recording, storage and replay (forward or reverse) are also available either by exact acquisition and reproduction of a series of points in the space, or provided via automatic path generation.
Given a start point for a path (even with some pass-through points and an end point) the kinematic engine of the Remote Robot automatically computes a safe path to drive the
robot, through all of the given points, avoiding collisions with surrounding obstacles.
Gripper status (active or Inactive) is included in path recording, allowing manual teaching for object pick-up, together with motions and back to replay.
Remote
Robot can also act as a visive remote monitoring tool for a working cell that runs with standard
robot programs.
In order to operate Remote
Robot needs only a dedicated LAN (100Mb) connection with the
robot controller; virtually any type of
robot can be supported and users can build their own environment using 3D models or parametric objects.
Main Features
- Three-dimensional virtual environment model for real-time collision check
- Multiple driving modes: axis, cartesian world, cartesian tool, cartesian frame
- Automatic path calculation
- Path storage for future playback in forward/reverse mode
- Intuitive motion thanks to the view-relative motion mode
- Multiple camera view for real environment monitoring
- Visive monitoring of a remote working cell
- Handling gripper supported
Remote Robot desktop console
Remote
Robot 1.0 is equipped with a personal computer featuring:
Operating System Windows 2000 Pro or XP Pro
CPU Pentium 4 2.8 GHz
SVGA NVidia GE-Force 4 128MB or equivalent
RAM DDRAM 512 Mbytes
Hard Disk 20 Gbytes
Dual network interface cards Intel/3Com T100 or equivalent
Monitor 15" TFT with resistive touch screen